What Is a Differential Pressure Transmitter?
A differential pressure transmitter is a device used to measure the difference in pressure between two points in a fluid-filled system. It's a type of pressure sensor commonly used in industrial processes to monitor and control various parameters such as flow, level, or density of liquids and gases.
Here's how it works:
Pressure Sensing: The transmitter consists of two pressure sensing elements, one exposed to each of the pressure points being measured. These elements are designed to sense the pressure applied to them and convert it into an electrical signal.
Calculation of Pressure Difference: By comparing the pressure sensed by the two elements, the transmitter calculates the pressure difference between the two points. This difference in pressure is crucial in various applications, such as determining the level of liquid in a tank or the flow rate of a fluid through a pipe.
Output Signal: The transmitter then produces an output signal, usually in the form of an electrical current (such as 4-20 mA) or a voltage signal. This signal is proportional to the pressure difference and can be interpreted by control systems or monitoring devices.
Calibration and Accuracy: Differential pressure transmitters need to be calibrated to ensure accuracy. Calibration involves adjusting the transmitter to match its output signal with the actual pressure difference it measures. Regular calibration is necessary to maintain precision over time.
These transmitters find applications in various industries, including chemical processing, oil and gas, water treatment, HVAC systems, and more. They are vital for processes where precise control and monitoring of fluid pressures are essential for operational efficiency and safety.
The Anatomy of a Differential Pressure Transmitter
To comprehend its functionality, envision a sophisticated apparatus comprising diaphragms, sensors, and electronic circuits. When pressure disparities occur, the diaphragms within the transmitter deform, generating electrical signals. These signals, once processed by the internal circuitry, transform into meaningful data for analysis.
Applications Across Industries
Differential pressure transmitters find applications in diverse sectors. In the petrochemical industry, they monitor gas flow rates with precision. In HVAC systems, they ensure optimal airflow. Even in healthcare, these transmitters facilitate accurate readings in respiratory equipment.
Advantages of Differential Pressure Transmitters
Precision and Accuracy: Differential pressure transmitters deliver highly accurate measurements, crucial for processes where precision is non-negotiable.
Versatility: Their adaptability to various mediums, such as gases and liquids, makes them indispensable across industries.
Real-time Monitoring: The real-time data they provide enables prompt adjustments, ensuring processes run seamlessly.
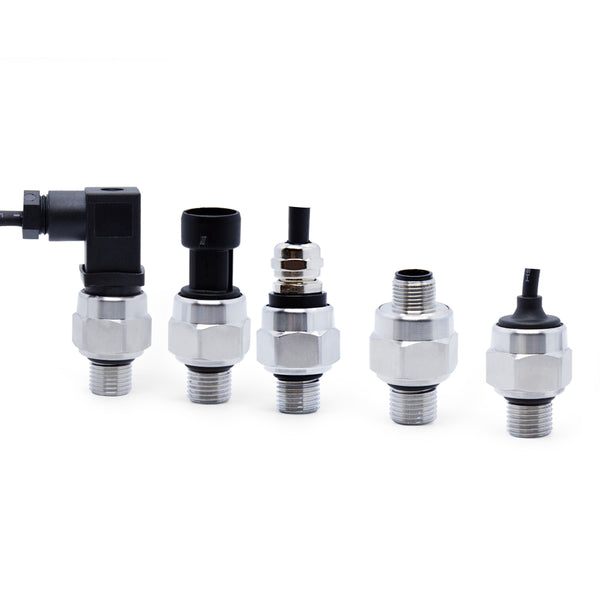
FAQs About Differential Pressure Transmitters
How does a differential pressure transmitter function?
A differential pressure transmitter is a device used to measure the difference in pressure between two points in a fluid-filled pipe or vessel. It operates based on the principle that as the pressure difference between two points changes, it causes a deflection in a sensing element, which is then converted into an electrical signal. Here's a step-by-step explanation of how it functions:
Pressure Sensing Element: The transmitter consists of a pressure sensing element, often a diaphragm or a bourdon tube, which deforms under the influence of pressure. When there is a difference in pressure between the high-pressure (H) and low-pressure (L) ports, this element deforms accordingly.
High-Pressure (H) and Low-Pressure (L) Ports: The H and L ports of the transmitter are connected to the points in the pipe or vessel where the pressure difference needs to be measured. The H port is exposed to higher pressure, and the L port is exposed to lower pressure.
Deflection of Sensing Element: When there is a pressure difference between the H and L ports, the sensing element deforms. The extent of this deformation is proportional to the difference in pressure.
Electrical Conversion: The deforming sensing element is usually connected to a mechanism that converts this mechanical movement into an electrical signal. This can be done through various means, such as strain gauges attached to the sensing element. As the element deforms, the resistance of the strain gauges changes, creating a proportional electrical signal.
Output Signal: The electrical signal generated is then sent to the transmitter circuitry. This signal is typically a direct current (DC) voltage or current, proportional to the pressure difference detected by the sensing element.
Signal Conditioning: The electrical signal might be conditioned and amplified to ensure accuracy and reliability. Signal conditioning can involve processes like filtering out noise and adjusting the signal strength.
Transmission and Display: The conditioned signal is transmitted to a control system or a display unit where it can be further processed, monitored, or recorded. In industrial applications, this information is often used for process control, monitoring, and automation.
In summary, a differential pressure transmitter functions by translating the mechanical deformation of a sensing element, caused by the pressure difference between two points, into an electrical signal. This signal can then be utilized for various industrial and scientific purposes, providing valuable information about the process conditions.
What distinguishes a differential pressure transmitter from other pressure measuring devices?
Unlike standard pressure sensors, differential pressure transmitters compare pressure variances, offering nuanced insights into fluid dynamics.
Can a differential pressure transmitter be used with corrosive substances?
Yes, specialized variants made of corrosion-resistant materials are available, ensuring compatibility with corrosive mediums.
Are differential pressure transmitters suitable for high-pressure environments?
Absolutely. There are models designed to withstand extreme pressure conditions, making them ideal for applications in high-pressure industrial setups.
What maintenance do these transmitters require?
Regular calibration and occasional inspection are necessary to maintain optimal performance and accuracy.
Can differential pressure transmitters be integrated into automated systems?
Certainly. Their compatibility with automation systems enhances efficiency by providing real-time data for automated decision-making.
Conclusion
In essence, understanding what a differential pressure transmitter is unlocks a world of possibilities in various industries. Its intricate design, coupled with remarkable precision, makes it a cornerstone of modern engineering. Embracing its capabilities empowers industries to operate with unprecedented accuracy and efficiency.
Leave a comment